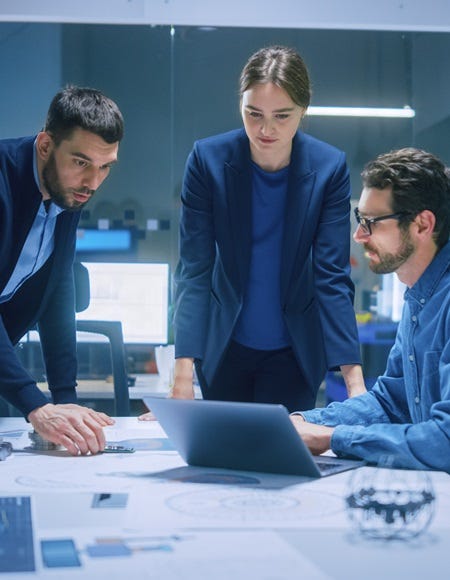
Strukturierte Fehlerbehebung für höchste Qualität: der 8D-Report in der Praxis.
Hinweis: Diese Vorlesefunktion verwendet eine synthetisch erzeugte Stimme aus einem KI-System.
Die Stimme ist keine Aufnahme einer realen Person.
Stellen Sie sich vor, ein Hersteller erhält plötzlich eine Reklamation von einem wichtigen Kunden: Ein Serienfehler in einem Produkt führt zu Ausfällen und beschädigt das Vertrauen. Der erste Reflex ist oft, das Problem schnell zu beheben und die Auswirkungen zu minimieren. Doch ohne eine tiefergehende Analyse könnte der Fehler erneut auftreten – mit noch gravierenderen Folgen.
Genau hier kommt der 8D-Report ins Spiel. Anstatt sich nur mit den Symptomen abzufinden, fordert die 8D-Methode von Qualitätsmanagern, die wahren Ursachen zu identifizieren und langfristige Lösungen zu entwickeln. Es ist ein bewährtes Instrument, das Unternehmen nicht nur hilft, akute Probleme zu lösen, sondern gleichzeitig die Grundlage für eine nachhaltige Qualitätskultur schafft.
Dieser Blogbeitrag erläutert die 8 Disziplinen des Report. Ein Anwendungsfalls für Qualitätsverantwortliche in der Fertigungsindustrie (Automobilzulieferer) liefert Praxisbezug.
Was ist ein 8D-Report?
Ein 8D-Report (8-Disziplinen-Report) ist ein standardisiertes Dokumentations- und Problemlösungsformat, das dazu dient, Fehler und Abweichungen systematisch zu bearbeiten. "8D" steht dabei für die acht Schritte (Disziplinen), die durchlaufen werden müssen, um ein Problem vollständig zu verstehen und dauerhaft zu beheben. Jeder dieser Schritte hat klare Zielsetzungen und führt zu spezifischen Ergebnissen, die im 8D-Report dokumentiert werden.
Ursprünglich entwickelt in der Automobilindustrie, hat sich der 8D-Report inzwischen als anerkannter Industriestandard etabliert. Unternehmen aus dem Maschinenbau, der Medizintechnik, der Elektronikbranche und vielen weiteren Bereichen nutzen ihn zur strukturierten Reklamationsbearbeitung und internen Fehleranalyse.
Das Ziel der 8D-Methode ist es nicht nur, einzelne Fehler zu korrigieren, sondern die Organisation als Ganzes resilienter und lernfähiger zu machen.
Die acht Disziplinen des 8D-Reports im Überblick.
Ein vollständiger 8D-Report gliedert sich in acht klar definierte Schritte. Ergänzend wird in manchen Standards eine vorbereitende Phase D0 durchgeführt. Um die Wirksamkeit der 8D-Methode voll auszuschöpfen, ist es entscheidend, die einzelnen Schritte nicht als reine Formalitäten zu betrachten. Jeder Schritt stellt ein wichtiges Element des gesamten Problemlösungsprozesses dar.
Im Folgenden erläutern wir die einzelnen Disziplinen detailliert und zeigen, worauf es in der praktischen Umsetzung besonders ankommt.
D0: Problem bestätigen und 8D-Prozess einleiten.
Bevor die eigentliche Problemlösung beginnt, wird das Problem verifiziert und bewertet. Dieser vorbereitende Schritt dient dazu, die Dringlichkeit zu beurteilen, erste Informationen zu sammeln und die formelle Einleitung des 8D-Prozesses durch das Qualitätsmanagement zu initiieren.
D1: Team zusammenstellen.
Probleme entstehen selten an einer einzigen Stelle. Ebenso wenig können sie von einer einzelnen Person gelöst werden. Genau deshalb beginnt ein effektiver 8D-Report mit der Bildung eines interdisziplinären Teams.
In der Praxis zeigt sich oft: Je komplexer das Problem, desto wichtiger ist es, unterschiedliche Fachrichtungen und Hierarchieebenen einzubeziehen. Idealerweise setzt sich das Team aus Mitarbeitenden der betroffenen Produktionslinie, der Qualitätssicherung, der Entwicklung und, falls relevant, des Einkaufs zusammen. Diese Vielfalt ermöglicht es, verschiedene Blickwinkel auf das Problem zu werfen und so die tatsächlichen Ursachen schneller zu erkennen.
Entscheidend ist nicht nur die fachliche Kompetenz der Teammitglieder, sondern auch ihre Fähigkeit, zusammenzuarbeiten. Eine klare Rollenverteilung und eine offene Kommunikation helfen, die Teamarbeit effizient zu gestalten. Schon zu Beginn sollte festgelegt werden, wer die Verantwortung für die Koordination und die Dokumentation der Ergebnisse übernimmt.
Beispiel D1: Team zusammenstellen
Ein interdisziplinäres Team wird gebildet bestehend aus:
- Qualitätsmanagement (Leitung)
- Fertigungsleitung
- Konstruktion
- Lieferantenmanagement
- Wareneingangsprüfung
D2: Problem beschreiben.
Viele Fehlerursachen bleiben unentdeckt, weil das eigentliche Problem nicht präzise beschrieben wird. Eine unklare Definition kann dazu führen, dass Ressourcen falsch eingesetzt und Maßnahmen ins Leere laufen.
Im zweiten Schritt wird daher das Problem klar und vollständig erfasst. Dabei geht es nicht nur um die Beschreibung der Symptome, sondern auch um die Erfassung der betroffenen Produkte, Seriennummern, Prozesse und Umweltbedingungen. Fragen wie „Wann genau tritt der Fehler auf?“ oder „Ist das Problem reproduzierbar?“ helfen, die Grenzen des Problems sauber abzustecken.
In vielen Unternehmen hat es sich bewährt, die Problemstellung in Daten, Fakten und visuelle Darstellungen zu übersetzen. Grafiken, Fehlerbilder oder Diagramme bieten oft schneller ein klares Bild als lange Textbeschreibungen.
Beispiel D2: Problem beschreiben
Bei 7 % der gelieferten Motorgehäuse (Teilenummer: MG-4310) wurden fehlerhafte Bohrungen festgestellt. Der Durchmesser weicht um mehr als 0,3 mm vom Toleranzbereich ab, was die Montage des Zylinderkopfes verhindert.
- Wann? Seit dem 02.05.2025
- Wo? Montagelinie 3, Werk B
- Wie viele? 37 von 530 Gehäusen in KW18 betroffen
- Sichtbare Auswirkungen: Störung in der Endmontage, Stillstandszeit von 1,5 Stunden
D3: Sofortmaßnahmen einleiten.
Während die Ursachenanalyse noch läuft, muss verhindert werden, dass sich das Problem weiter ausbreitet oder Kunden betroffen sind. Die Sofortmaßnahmen im 8D-Prozess dienen dazu, Zeit zu gewinnen und Schäden zu begrenzen.
In der Praxis bedeutet das oft, betroffene Produkte zu sperren, zusätzliche Prüfungen einzuführen oder alternative Prozesse zu nutzen. Wichtig dabei: Jede Maßnahme muss dokumentiert und überwacht werden. Nur so kann später nachvollzogen werden, welche Aktionen erfolgreich waren und welche nicht.
Eine Herausforderung ist dabei häufig, Sofortmaßnahmen so zu gestalten, dass sie die Produktion nicht unnötig belasten. Ein kluges Gleichgewicht zwischen Sicherheit und Effizienz ist gefragt.
Beispiel D3: Sofortmaßnahmen einleiten
- Rückhaltung aller noch nicht montierten Motorgehäuse
- 100 %-Kontrolle der eingehenden Teile durch Wareneingang
- Umleitung der betroffenen Teile zur manuellen Nachbearbeitung
- Info an Kunden zur Transparenz
D4: Fehlerursache identifizieren.
Hinter jedem Fehler steht eine Geschichte und sie ist oft komplexer als auf den ersten Blick ersichtlich. Die Ursachenanalyse ist das Herzstück des 8D-Reports, denn nur wenn die wahre Ursache gefunden wird, kann das Problem nachhaltig gelöst werden.
Ein häufiges Problem in der Praxis ist der sogenannte "Symptom-Fix": Maßnahmen werden eingeleitet, ohne die wahre Ursache zu beseitigen. Um das zu vermeiden, wird im Rahmen der Ursachenanalyse systematisch und datenbasiert gearbeitet.
Bewährte Methoden wie die 5-Why-Technik helfen, immer tiefer nach der Wurzel des Problems zu graben. Dabei wird durch wiederholtes Nachfragen des „Warum?“ (in der Regel fünfmal) die wahre Ursache schrittweise freigelegt. Ergänzend dazu bietet das Ishikawa-Diagramm (Fischgrätendiagramm) eine strukturierte Visualisierung potenzieller Einflussfaktoren wie Mensch, Maschine, Material, Methode und Umwelt.
Ein häufiger Fehler ist, nur die "offensichtliche" Ursache zu identifizieren. Ein professionelles Team prüft Hypothesen kritisch, sammelt belastbare Beweise und vermeidet voreilige Schlüsse. Nur so kann sichergestellt werden, dass die späteren Maßnahmen tatsächlich greifen.
Beispiel D4: Fehlerursache identifizieren
Ursachenanalyse (Ishikawa + 5-Why):
- Der Fehler tritt nur bei Bauteilen auf, die von einem neuen Lieferanten stammen.
- Die CNC-Bohrmaschine war nicht korrekt kalibriert (Fehlbedienung beim Rüsten).
- Bediener hat Prüfprotokoll nicht ordnungsgemäß geführt: keine Erkennung.
Hauptursache: Fehlende Kalibrierprüfung nach Werkzeugwechsel und unzureichende Schulung des Lieferantenpersonals.
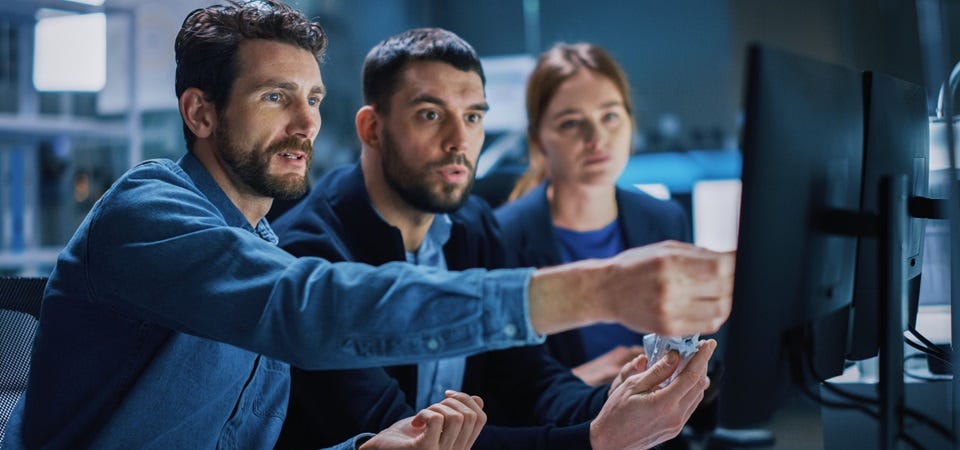
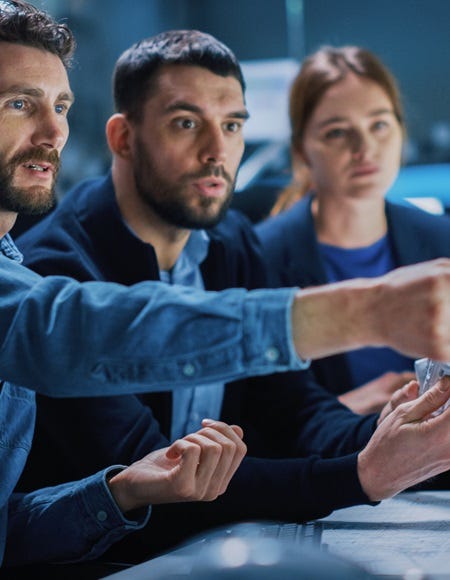
D5: Korrekturmaßnahmen definieren.
Sobald die Ursachenanalyse abgeschlossen ist, beginnt die eigentliche Problemlösung. Dauerhafte Abstellmaßnahmen müssen so gestaltet sein, dass sie direkt an der Hauptursache ansetzen.
Hier zeigt sich oft der Unterschied zwischen einem oberflächlichen und einem professionellen 8D-Report: Wirkungsvolle Maßnahmen gehen nicht den Weg des geringsten Widerstands, sondern stellen sicher, dass der Fehler unter vergleichbaren Bedingungen nicht wieder auftreten kann.
Dauerhafte Lösungen können
- technischer Natur sein: etwa durch konstruktive Änderungen,
- organisatorischer Art sein: etwa durch optimierte Prüfpläne oder
- prozessbezogen sein: zum Beispiel durch strengere Prozesskontrollen.
Wichtig ist, dass die Maßnahmen klar definiert, terminiert und hinsichtlich der Verantwortlichkeiten zugewiesen werden.
Beispiel D5: Korrekturmaßnahmen definieren
- Sofortige Neukalibrierung der Bohrmaschinen beim Lieferanten
- Überarbeitung der Arbeitsanweisung für den Rüstvorgang
- Einführung einer zusätzlichen Zwischenprüfung nach jedem Werkzeugwechsel
- Schulung aller Bediener des Lieferanten durch QM-Abteilung
D6: Korrekturmaßnahmen umsetzen.
In der Praxis ist die Umsetzung von Maßnahmen häufig der kritischste Punkt im 8D-Prozess. Was auf dem Papier gut klingt, muss im Alltag unter realen Bedingungen bestehen.
Deshalb wird jede Maßnahme im Anschluss an die Implementierung auf ihre tatsächliche Wirksamkeit geprüft. Dabei werden gezielt Daten gesammelt: Treten Fehler weiterhin auf? Verändert sich die Fehlerhäufigkeit? Können externe und interne Reklamationen reduziert werden?
Eine einfache Überprüfung reicht oft nicht aus. Stattdessen sollte ein Zeitraum definiert werden, innerhalb dessen die Wirksamkeit beobachtet wird. Nur wenn die Ergebnisse klar belegen, dass das Problem dauerhaft gelöst wurde, kann der 8D-Report abgeschlossen werden.
Beispiel D6: Korrekturmaßnahmen umsetzen
- Umsetzung am 08.05.2025 abgeschlossen
- Vor-Ort-Audit beim Lieferanten durch QM-Team am 09.05.2025
- Nachproduktion von 200 Gehäusen fehlerfrei durch 100 %-Prüfung bestätigt
D7: Fehlerwiederholung verhindern.
Ein erfolgreicher 8D-Report löst nicht nur ein einzelnes Problem, sondern trägt zur systematischen Weiterentwicklung des gesamten Unternehmens bei.
Nach Abschluss der Maßnahmen wird überprüft, welche systemischen Schwächen das Problem überhaupt ermöglicht haben. Typische Ansätze zur Vermeidung zukünftiger Fehler sind die Anpassung von Designvorgaben, verbesserte Schulungen, zusätzliche Prüfmechanismen oder die Überarbeitung von Lieferantenanforderungen.
Der große Mehrwert liegt darin, nicht nur zu reagieren, sondern proaktiv Strukturen zu verbessern. So wird Qualitätssicherung zu einem strategischen Erfolgsfaktor.
Beispiel D7: Fehlerwiederholung verhindern
- Aktualisierung der Lieferantenvorgaben in der Qualitätssicherungsvereinbarung
- Aufnahme des Kalibrierprotokolls als Pflichtdokument im Wareneingang
- Prozessfreigabe durch PPF (Produktionsprozess- und Produktfreigabe)
- Interne Lessons Learned in FMEA-Datenbank aufgenommen
D8: Team und Leistung anerkennen.
Der Abschluss eines 8D-Reports ist ein bedeutender Moment: Nicht nur, weil ein Problem gelöst wurde, sondern auch, weil alle Beteiligten daraus gelernt haben.
Die vollständige Dokumentation der Ergebnisse, der Analysewege und der getroffenen Maßnahmen stellt sicher, dass die Organisation auch bei ähnlichen Herausforderungen schneller und besser reagieren kann. Gleichzeitig sollte das Team für seine Arbeit Anerkennung erhalten. Wertschätzung und positives Feedback stärken die Motivation und tragen zu einer gelebten Fehler- und Verbesserungskultur bei.
Beispiel D8: Team und Leistung anerkennen
- Dank und kurze Präsentation im wöchentlichen QM-Meeting
- Hervorhebung der schnellen Problemlösung im monatlichen Bericht an die Geschäftsleitung
- Lieferant wurde positiv erwähnt und eingeladen zum nächsten Lieferantenworkshop
Fazit.
Ein professionell geführter 8D-Report reduziert nicht nur akute Fehlerkosten, sondern steigert auch die Effizienz und Innovationskraft des Unternehmens.
Interne Abläufe werden transparenter, Schwachstellen systematisch abgebaut und das Qualitätsbewusstsein auf allen Ebenen gestärkt. In Summe führen diese Effekte zu einer nachhaltig höheren Kundenzufriedenheit und einer besseren Marktposition.
Sieben Praxistipps für den erfolgreichen Einsatz des 8D-Reports.
- Frühzeitig starten: Warten Sie nicht zu lange – je früher der 8D-Prozess beginnt, desto gezielter können Schäden begrenzt werden.
- Das richtige Team bilden: Stellen Sie ein interdisziplinäres Team mit klaren Rollen zusammen. Vielfalt im Team führt zu besseren Lösungen.
- Symptome nicht mit Ursachen verwechseln: Hinterfragen Sie jede Annahme kritisch und setzen Sie auf bewährte Analysemethoden wie „5 Why“ oder Ishikawa.
- Visuelle Hilfsmittel nutzen: Bilder, Diagramme und Daten helfen, Probleme besser zu verstehen und im Team zu kommunizieren.
- Maßnahmen konkret definieren: Formulieren Sie klare, nachvollziehbare Maßnahmen – mit Verantwortlichen und Terminen.
- Wirksamkeit prüfen: Messen Sie, ob Maßnahmen langfristig greifen. Erst dann gilt das Problem als gelöst.
- Lerneffekte sichern: Nutzen Sie die Erkenntnisse aus dem Report zur systemischen Verbesserung, z. B. in Schulungen oder Standards.
Empfehlung.
Erfahren Sie in unserem Seminar 8D-Report und Ursachenanalyse, wie Sie mit der 8D-Methode Qualitätsprobleme nachhaltig und effizient lösen können. Anhand praxisnaher Beispiele lernen Sie, Ursachen systematisch zu analysieren, Maßnahmen gezielt umzusetzen und Ihren Verbesserungsprozess dauerhaft zu optimieren.
Perfekt für Verantwortliche im QM und Reklamationswesen, die ihre Kompetenzen stärken möchten. Hier mehr zum Seminar erfahren.